Discover how recycled base oils are re‑refined, their differences from virgin stocks, detection methods, odor, performance in lubricants, and impact on oil pricing.
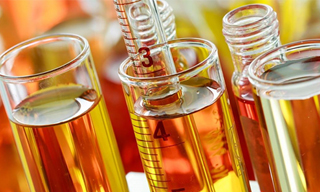
Summary
Re‑refining of used lubricants employs physical and chemical steps—vacuum distillation, solvent extraction, hydrotreating, acid‑clay treatment, thin‑film evaporation—to remove water, light ends, metals, polar compounds and aromatics. Among these, hydrotreating delivers the highest quality (meets API Group II specs) but at greater cost and hydrogen consumption, while solvent extraction is lowest‑cost and efficient at recovering 78–85% base oil yield . Molecularly, virgin Group II stocks are narrowly distilled paraffinic chains (C20–C50, >95% saturates), whereas re‑refined oils show broader chain distributions (C15–C65), higher aromatics and sulfur remnants. For identification, two‑dimensional GC×GC–TOFMS provides the most definitive fingerprinting, though FTIR plus elemental (ASTM D6481) is a cost‑effective lab solution.
1. Methods of Base Oil Recycling
Re‑refining follows these core stages:
Dewatering & Dewaxing – Remove free water and wax via heating and clay treatment.
Vacuum Distillation – Separate light ends and heavy residues under high vacuum.
Purification – Apply one or more of:
Solvent Extraction (phenol, furfural, NMP)
Hydrotreating (high‑pressure H₂ + catalyst)
Acid‑Clay Treatment (sulfuric acid + clay)
Thin‑Film (Wiped‑Film) Evaporation
Finishing – Adsorption (clay, silica), deodorization, dewaxing.
1.1 Detailed Comparison of Key Processes
Criterion | Solvent Extraction | Hydrotreating | Acid‑Clay Treatment | Thin‑Film Evaporation |
---|---|---|---|---|
Removal Efficiency | Removes >90% aromatics & polar (solvent‑solubility) | Removes aromatics, sulfur, nitrogen to <50 ppm | Removes metals & sludge; less effective on light ends | Excellent heavy residue removal; moderate polar removal |
Yield (%) | 78–82% | 80–90% | 75–85% | 84–88% |
Product Quality | Group I‑II quality | Group II (meets API II) | Group I | Group I |
Capital & Operating Cost | Moderate equipment; solvent regen | High‑pressure reactors; H₂ sourcing | Low capital; high waste sludge | High vacuum, wiped‑film units |
Environmental Footprint | Solvent recovery emissions risk | H₂ production energy; low emissions post | Acid neutralization waste | Energy‑intensive vacuum |
Scalability | Highly scalable | Scalable but complex | Limited by waste handling | Medium; specialized units |
Best Overall: Hydrotreating, for purity, stability, and API compliance, despite higher cost.
Best Cost‑Effective: Solvent extraction, balances performance and economics .
2. Molecular & Structural Differences
2.1 Chain Length & Saturation
Virgin Group II Base Oils: Highly paraffinic, narrow cut from C₂₀–C₅₀, >95% saturated straight chains, VI >110, sulfur <50 ppm.
Re‑Refined Oils: Broader cut C₁₅–C₆₅, saturates 90–95%, aromatics 5–10%, sulfur 100–500 ppm, VI 90–105 .
2.2 Molecular Complexity
Aromatics & Branched Chains: Re‑refined contain trace polycyclic aromatics (PAHs) and branched isoparaffins from recycle streams.
Polar Compounds: Sulfoxides and nitrogen heterocycles residual in recycling; removed in hydrotreating but persist in solvent‑only processes.
3. Detection & Laboratory Identification
Accurate differentiation relies on combining chromatographic and spectroscopic assays.
3.1 Candidate Methods
Technique | Target Analytes | Sensitivity & Specificity | Cost & Accessibility | Turnaround Time |
---|---|---|---|---|
GC×GC–TOFMS | Detailed fingerprint (PAHs, n‑alkanes, iso‑alkanes) | Highest – resolves co‑elution | High capital, specialist | 1–2 days |
GC–MS | Hydrocarbon distribution, PAHs | High – general profiling | Moderate lab equipment | 1 day |
FTIR (ASTM D7414) | Sulfoxide, carbonyl, aromatics | Moderate – functional groups | Low cost, widespread | Hours |
Elemental XRF or ICP (ASTM D6481) | S, N, metals | High – low ppm detection | Moderate | Hours |
NMR Spectroscopy | Detailed structural isomers | High – research labs only | Very high cost | Days |
3.2 Recommended Solution for Customers
For routine quality control and authenticity testing, a two‑step approach is ideal:
FTIR Screening (ASTM D7414) to flag unexpected aromatics/sulfoxides within hours.
GC–MS Confirmation (ASTM D2887 or D5186) to profile hydrocarbon cuts and detect recycled fingerprints within 24 hours.
If ultra‑high certainty is required (e.g., regulatory audit), deploy GC×GC–TOFMS for the definitive fingerprint—though cost and expertise limit its routine use .
Key Takeaways:
Hydrotreating yields the purest re‑refined oils, while solvent extraction offers best cost/efficiency balance.
Virgin base oils are narrow‑cut, nearly 100% saturated (C₂₀–C₅₀); recycled oils span broader chains with residual aromatics.
FTIR + GC–MS is the most practical lab protocol; GC×GC–TOFMS is reserved for definitive forensic analysis.
Use in Motor and Industrial Oils
Yes, re‑refined base oils are used in both motor and industrial lubricants. When formulated with appropriate additive packages, they can meet API and ACEA specifications for passenger cars, heavy‑duty diesels and industrial machinery. Compared to virgin stocks:
Performance: Slightly lower oxidation stability and VI, requiring more antioxidants and VI improvers.
Cost: Typically 10–30% lower raw material cost, passing savings to consumers.
Sustainability: Up to 80% lower carbon footprint versus virgin refining.
Motor Oil Pricing and Base Oil Source
Lower‑priced motor oils often incorporate Group I or re‑refined base oils, whereas premium oils use Group II+ virgin stocks or synthetics (Group III/IV). The base oil category (mineral vs. synthetic, virgin vs. re‑refined) accounts for up to 70% of formula cost, so re‑refined stocks can significantly reduce retail prices.
Conclusion
Re‑refining used lubricants into high‑quality base oils not only conserves valuable resources but also slashes greenhouse gas emissions—re‑refined oils can deliver up to 70 % fewer CO₂ emissions compared to virgin stocks, significantly lowering the carbon footprint of lubrication systems . While solvent extraction offers an optimal balance of cost and performance, advanced hydrotreating processes yield API Group II–compliant base oils indistinguishable from virgin paraffinic stocks in purity and stability. Life‑cycle assessments report 50–90 % reductions in environmental impact for re‑refining versus conventional refining, underscoring the process’s role in sustainable manufacturing . Embracing re‑refined base oils fosters circular economy principles—minimizing crude oil extraction, reducing waste, and promoting resource efficiency throughout the lubricant value chain.
Industry momentum is evident as original equipment manufacturers and fleet operators adopt circular lubricants to meet stringent environmental regulations and bolster supply‑chain resilience. Regulatory incentives and subsidies, notably in regions like California and Europe, further accelerate re‑refining capacity growth and closed‑loop recycling initiatives . Market analyses project robust expansion of the re‑refined base oil sector, driven by mounting environmental mandates and the economic appeal of lower feedstock costs . Moreover, the integration of cutting‑edge chromatographic and spectroscopic analytics ensures that re‑refined products consistently meet rigorous quality standards, reinforcing customer confidence in recycled oils.
By embracing these advanced re‑refining technologies, manufacturers and end‑users can unlock substantial cost savings—often 10–30 % in raw material expenses—while upholding the highest performance benchmarks for motor and industrial lubricants. As regulatory landscapes evolve and technological innovations mature, re‑refined base oils will stand at the forefront of a greener, more cost‑effective lubrication future—driving both environmental stewardship and industrial excellence into the next generation of lubricant production.